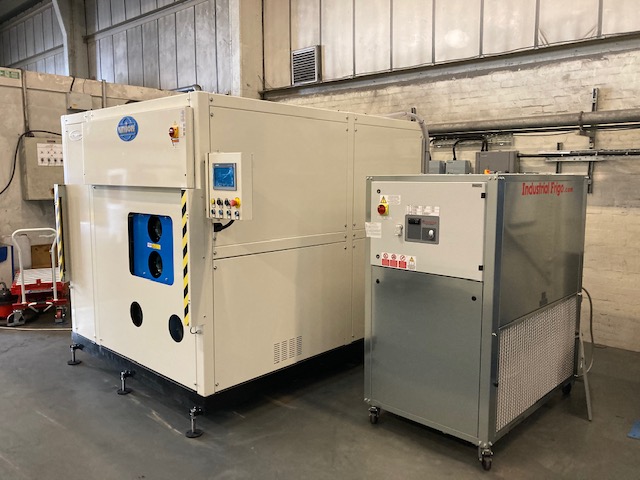
Wheelabrator Case Study - Union MDMV2
Case Study: Wheelabrator Impact Finishers Adopts Safer, Compliant Cleaning with Union & SAFECHEM
Industry: Aerospace, Automotive, Oil & Gas, Architecture
Client: Wheelabrator Impact Finishers (Part of the Norican Group)
Solution Providers: SAFECHEM, D&S Ultra-Clean Ltd.
Challenge: Replacement of banned n-propyl bromide (nPB)
Solution: Union MDMV2 PX Closed Cleaning System with DOWPER™* MC & SAFE-TAINER™ System
Result: Regulatory compliance, improved safety, and customer-accepted cleaning performance
Background
Wheelabrator Impact Finishers, part of the Norican Group, has over 50 years of expertise delivering high-quality subcontract shot peening services. Serving sectors such as aerospace, automotive, motorsport, architecture, and general engineering, the company supports customers in increasing the fatigue life of high-stress, lightweight alloy components critical to modern aircraft and automotive performance.
Aerospace shot peening components processed include everything from large wing ribs and undercarriage parts to aero engine fan blades and compressor components—all requiring exceptional levels of cleanliness post-processing.
The Challenge
Historically, Wheelabrator used n-propyl bromide (nPB) in open dip tanks for post-process cleaning. However, with nPB being identified as a Substance of Very High Concern (SVHC) under REACH and its sunset date set for July 4, 2020, the company urgently needed a safe, compliant alternative.
Manual wiping was also required to complete cleaning—time-consuming, labour-intensive, and presenting occupational exposure risks.
“The safety of our working staff is absolutely paramount. At the same time, the solution should be cost-efficient, reliable, and accepted by our customer base – including Airbus and Boeing.”
— Ron Orchard, Production Manager, Wheelabrator
The Solution
In early 2020, Wheelabrator partnered with SAFECHEM and D&S Ultra-Clean Ltd., the UK distributor for Union S.p.a., a leading manufacturer of precision cleaning systems.
Following evaluations, Wheelabrator selected the Union MDMV2 PX, a closed-loop vacuum cleaning system, to replace their open nPB setup. The machine was configured to operate with DOWPER™ MC*, a highly stabilized, virgin-grade perchloroethylene solvent supplied by SAFECHEM.
Why DOWPER™ MC and the SAFE-TAINER™ System?*
-
Widely accepted in aerospace: No additional customer approval required
-
Safe handling and environmental compliance: Thanks to the SAFE-TAINER™ closed-loop solvent delivery and collection system
-
Fast machine lead time: Critical given the approaching regulatory deadline
-
Local support: Installation and servicing provided by D&S Ultra-Clean Ltd. in the UK
“The educational work SAFECHEM has done around the safe usage of perchloroethylene gave us the confidence that DOWPER™* MC is the right product to go for.”
— Ron Orchard, Production Manager, Wheelabrator
The Outcome
Wheelabrator successfully transitioned to a closed, vacuum-based cleaning process that meets the stringent demands of their aerospace clients, improves worker safety, and ensures regulatory compliance.
-
Eliminated manual wiping steps
-
Improved process speed and consistency
-
Reduced solvent exposure risk
-
Maintained customer-accepted cleanliness levels
Conclusion
Wheelabrator’s proactive shift from nPB to a closed-loop cleaning system using DOWPER™ MC* and the SAFE-TAINER™ System demonstrates a robust response to evolving chemical regulations, while preserving product quality, operational efficiency, and workplace safety.